4 Best Practices for Industries to Get Value Out of Maintenance
- September 23, 2021
- Posted by: Sanket Pathak
- Categories: Digital Engineering, Quality Engineering, Thought Leadership
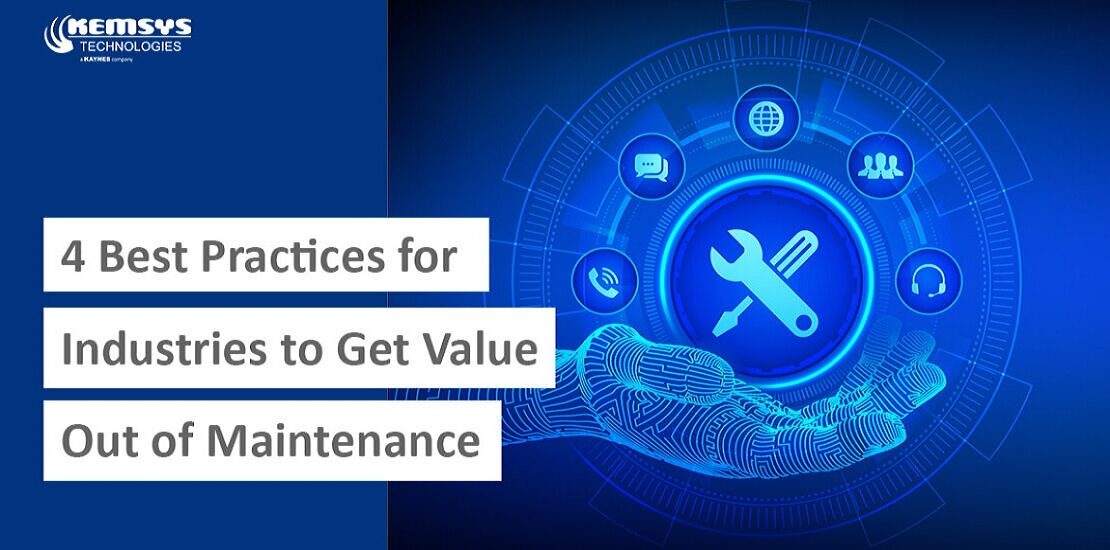
Every business or organization involved in manufacturing aims for operational efficiency. It aspires for high standards of uptime and reduced maintenance costs. If you’re an OEM, a machine/equipment breakdown could cost you or your customer as much as 10X the regular maintenance expenses.
Even otherwise, average maintenance cost ranges between 15% and 40% of the entire production costs . With so much riding on the perpetual functioning of manufacturing units and equipment, there must be a technique that helps organizations with maintenance just when needed to cut down on such mammoth maintenance costs.
Thankfully, there is and it’s called predictive maintenance. What stemmed from the recent tech advancements in the realm of Artificial Intelligence (AI), data science, and Machine Learning (ML), predictive analytics could now accurately predict when a machine/equipment could malfunction. The role of predictive maintenance doesn’t just stop with forecasting downtimes but goes an extra mile by initiating service requests from relevant teams or stakeholders autonomously.
This advancement or implementation has grabbed the attention of several manufacturing companies around the world.
Why wouldn’t it?
However, there’s more to it than what it seems. While predictive maintenance definitely helps in the minimization of machine/equipment downtime, there are some intricate concerns that are part of it. Most companies tend to overlook these and get carried away either by a superficial understanding of predictive analytics or just competition.
We are going to break this chain in today’s post as we will explore the challenges and shortcomings that stand in the way of scalable predictive maintenance and understand some best practices to unlock newer levels of efficiency as well.
The Different Levels of Predictive Maintenance Models
Predictive maintenance is a broad term and requires proper breakdown for comprehension purposes to understand the nuances in the system. For beginners, understand that there are four levels that differ in their tech requirements, scalability, and sophistication.
- Predictive Maintenance 1.0 or Condition-based maintenance – these units have sensors hooked onto the equipment that trigger alerts or alarms to notify of probable failure.
- Predictive Maintenance 2.0 or Equation-based maintenance – equations derived from previous failures help stakeholders and specialists come up with IoC (Indicators Of Compromise) points and help predict outcomes.
- Predictive Maintenance 3.0 or Fit-for-Purpose suites – sophisticated analytics and machine learning models generate or extract data from dedicated touchpoints and work on predicting malfunctions based on historical data.
- Predictive Maintenance 4.0 or Asset-wide analytics modules – an ecosystem of analytics modules and solutions monitor multiple systems simultaneously and provide insights to experts trained at incident response.
Let’s get started.
Challenges Involved in Large Scale Predictive Maintenance Programs
Substandard implementation of predictive models could ironically lead to an increase in downtime and associated costs. That’s why careful planning and strategizing are inevitable. Beyond these, there are also technical concerns involved in the process. Let’s look at what they are:
- Predictive modules thrive on data. The lack of quality data could skew results and make them ineffective in forecasting failure or breakdowns.
- If your predictive maintenance ecosystem has inaccurate sensors or if it suffers from poor infrastructure, the model would fail.
- The absence of the right talent pool or resources such as data scientists, annotators, and SMEs could limit your model from functioning at desired capabilities.
- If your resources are not trained well to work with sophisticated technology or when there’s a steep learning curve involved, the full potential of predictive models cannot be tapped into.
- Your aspirations should also consider and finalize the modules or units you wish to cover under predictive maintenance programs. Only those that hamper productivity and influence numbers (quality and revenue) should be included in the ecosystem.
4 Best Practices to Generate Value Out of Maintenance Models
Predictive maintenance is still mostly a buzzword among companies and stakeholders. They want to get hands-on with it and implement it for their machines/equipment without actually working out numbers, purposes, or returns. If you are at that stage, you would want to reconsider your aspirations and implement some of our recommendations and best practices. As an OEM, your organization is in a perennial manufacturing process, and with the right strategies to deploy predictive models, you could get more value out of maintenance systems.
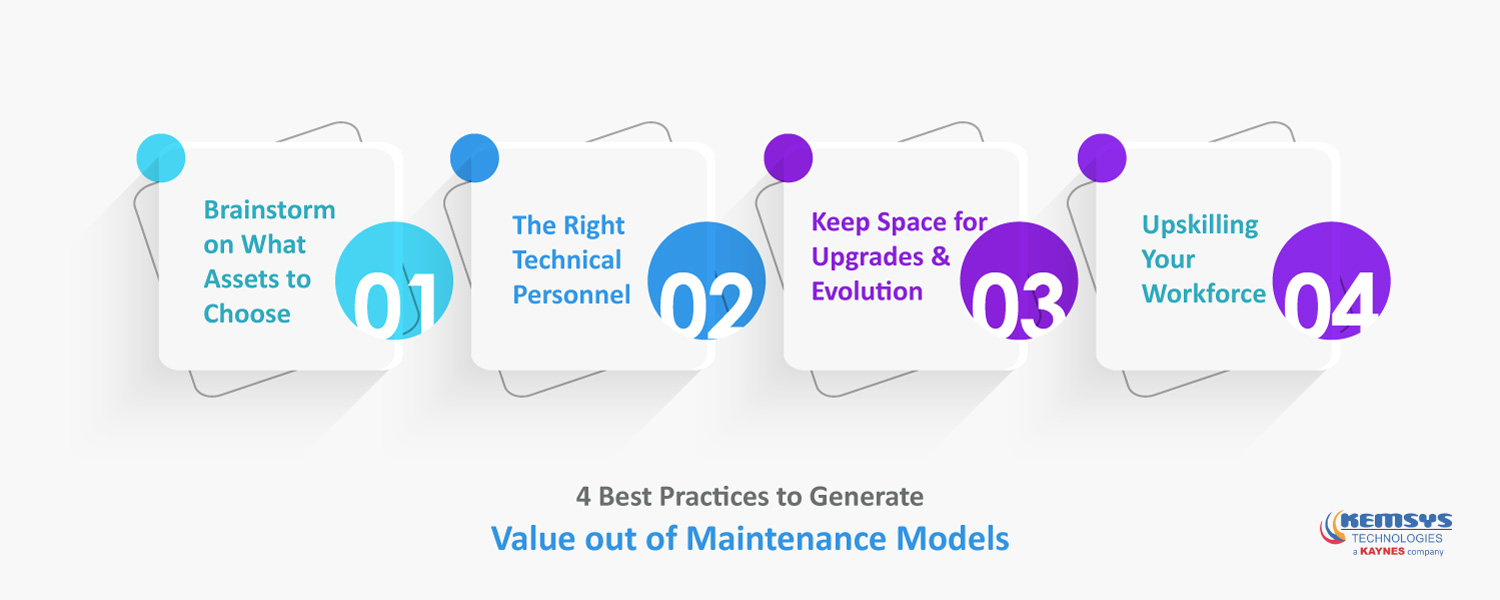
1. Brainstorm on What Assets to Choose
Choosing assets to be part of a predictive model ecosystem is the first step in overcoming challenges and shortcomings. This could prove to be a cost-effective way to eliminate consequences as you select only specific machines/equipment or units to be part of the solution suite.
To give you a better idea of how to do this, here’s an overview:
- Choose assets that are crucial for your operations and those that result in immediate erode revenue
- Prioritize assets that have adequate sensor range and data touchpoints
- Select assets that have frequent anomalies or malfunctioned in the past
2. The Right Tech Personnel
Predictive models are sophisticated and intricate in nature. Large-scale implementations of such concepts require the leadership of experts who know what they are doing and are aware of the consequences of their actions. Like you read, predictive maintenance models 3.0 and 4.0 are highly complex and to get meaningful value out of them, partnering with the right tech people is crucial.
A data scientist can help in the seamless transition of your organization, minimize the learning curve, reduce implementational expenses, choose the right tech stack and keep the entire system scalable (vertically). They can also tell you whether you should use SaaS models or build your own systems and take care of data and privacy-related legalities and compliances.
3, Keep Space for Upgrades and Evolution
Deploying a predictive maintenance program is not a one-time affair. It’s perennial just like your manufacturing units. Consistent optimization of systems, data touchpoints, resources, and more are essential to keep up with the increasing demands in your ecosystem. When this happens, your predictive model starts evolving into a solution that delivers precise results (minimize false positive and false negative ), captures numerous anomalies (recall value), and identifies concerns at a grassroots level.
4. Upskilling Your Workforce
We could classify the learning curve into two types – one that is associated with the knowledge of systems and operation of machines and the other that is quite abstract and revolves around the acclimatization to the newborn environment.
Our focus here is on the latter. When new systems and processes are introduced, the management also has the responsibility to ensure adequate roles and responsibilities are assigned to the right personnel and that transition from obsolete to sophisticated tools and units happen seamlessly.
Implementation can only be as effective as its plan and that’s why the focus should also be on nurturing and developing cross-functional teams, interoperable resources, and a workforce that can be quickly upskilled to tackle rising demands in data science and AI.
Wrapping Up
We believe you now have a better idea of how complex predictive maintenance models can be and what you need to consider before implementing them into your business. While these are not stoppers to your goals but just the fundamentals you need to know to realize your RoI from deploying advanced tools and systems.
We’re sure you’ll have a look into multiple aspects like the ones we’ve mentioned and pave the way for an operational environment that derives the best value out of its equipment and systems that take care of it.